potrebujete poradiť?
-
New cement standard EN 197-5
The cement industry in climate change
After years of wrangling, the new cement standard EN 197-5 was finally published.
New Cement Standard EN 197-5
Jan 18, 2022
After years of wrangling, the new cement standard EN 197-5 was finally published in July 2021. It defines framework conditions for a significant reduction of the clinker content in cements – an important step towards the goal of CO2 neutrality in concrete construction. MC already offers a broad range of products enabling even low-clinker concretes to produce the results required.
Cement is the most important construction material in the world, one which is virtually indispensable to any new build. Its key reaction with water is what binds sand and gravel together to create concrete. As essential as the building material is, its impact on man-made climate change is equally unequivocal.
Each metric ton of Portland cement represents 800 kg of CO2 released into the atmosphere
The combustion of the fossil fuels needed to heat a rotary kiln to more than 1,400 °C already gives rise to a fair amount of CO2. But this process causes just one third of the greenhouse gas emissions that ensue; two thirds of the carbon footprint attributable to classic cement come from the limestone or calcium carbonate that is burned as a raw material to make clinker. The chemical process behind this is called deacidification: The raw material calcium carbonate, CaCO3, decomposes during combustion to form clinker, CaO, plus CO2. If the two processes are taken together and the energy input of further processing, for example grinding the cement required into fine powder form, is added, the total of CO2 released per saleable metric ton the Portland cement comes in at around 800 kg.
Four billion metric tons of cement per year
Four billion metric tons of cement are manufactured worldwide every year. During this period, a typical cement plant produces an average of around one million metric tons of cement. Germany has more than 50 such facilities. But while there has been much discussion globally for years about climate-damaging aircraft flights, dirty coal-fired power plants or filthy diesel engines, the construction sector appears by comparison to have largely escaped public scrutiny. The primary reason: Currently, there are simply no alternatives to the use of cement in the construction industry. In Germany, for example, 30 million metric tons of cement was consumed in 2020 – causing the emission of around 24 million metric tons of CO2. By comparison: China uses over 2.5 billion metric tons of cement each year. The CO2 emissions arising from global cement production are so large that they are responsible for about eight percent of anthropomorphic greenhouse gas emissions worldwide – and thus for a bigger carbon footprint than global air traffic and all the data centres of the world put together. Given the rising demand in emerging markets such as India, Asia and Africa, this figure is likely to burgeon further in the coming years.
Objective: To reduce construction’s carbon footprint
Correspondingly huge efforts are being made to make the processes behind cement production more sustainable: The fossil fuels needed for firing have already been largely replaced by biomass-based alternatives with a lower CO2 footprint, and the efficiency of the associated processes has also been further optimised. The trend is towards cements in which the Portland content, also known as clinker, is reduced through the introduction of reactive or inert substances. This has resulted in a reduction in the clinker content to an average of 70% of the figure prevailing ten years ago.
New low-clinker cement groups
Around the world, research is being conducted to identify a range of alternatives to cement as the go-to material in building construction. However, the problem in manufacturing the quantities required appears unsolvable for the foreseeable future. So the route most likely to be adopted is that of significantly reducing the percentage of clinker in the kinds of cements that already exist today. And this is the approach adopted in the new cement standard EN 197-5. It describes two new cement classes, Portland-composite cements CEM II/C-M and composite cements of the grade CEM VI, which ensure the fitness for use of concrete structures despite their low clinker contents. The standard is the result of many years of research focusing specifically on the durability of low-clinker concretes. The idea behind their development is to grind the classic cement finer and “alloy” it with less reactive substances. Compared to classic Portland cement with its 95 % clinker content, the CEM II/C-M and CEM VI cements covered by EN 197-5 should enable the wider use of more clinker-efficient options as a step towards the goal of CO2 neutrality in concrete construction. For CEM II/C-M, the clinker content can be reduced to up to 50 % by mass and for composite cements in the CEM VI group to up to 35 % by mass.
For internal components and regular, classic external construction elements
It is clear that a cement with a full clinker content, i.e. Portland cement, performs differently from a cement in which the clinker content has been halved. This is reflected above all in early strength development and the rate of surface curing. The lower clinker content significantly slows down the hydration of the concrete. Although the newer concretes can be adjusted to a normal 28-day strength by grinding the cement particularly finely, some properties such as frost resistance or impermeability of the structure to penetrating media may decline as a result. Accordingly, although these cements are suitable for interior components and the normal classic exterior building element exposed to precipitation, they are not unconditionally applicable for all exposure classes. Hence application rules are currently being developed, with building authority approvals being issued ad hoc on the basis of individual investigations. For the main application of interior components and exterior building elements exposed to moderate frost, which account for around 70 % of the concrete market, the durability performance of clinker-reduced cements has already been proven, with considerable CO2 reduction potential likewise apparent.
Longer site times
However, the ideal case of the construction site concreting at 10 a.m. and striking the formwork at 10 a.m. the next day will certainly become the exception rather than the rule with particularly low-clinker cements, especially in low temperatures. That means the formwork will need to be left longer, with the result that both the construction site and scheduling will have to be organised differently in the future. The timeframe for achieving the climate goals is slowly becoming tighter in relation to cement production. Now the sector is starting to respond with more vigour due to cost pressures arising from CO2 certificates and other impending regulations. With the pricing of CO2 emissions now an established reality, the pressure on the cement industry to bring the new formulations to market is increasing; especially in Germany, where the new government elected in early autumn 2021 has, at least on paper, adopted a stricter climate policy and is also very likely to substantially force up future CO2 pricing. The measures that the industry has in the pipeline are, in fact, many and varied: Not only are the new, lower-clinker cements on the agenda, but also and above all clinker alternatives, non-fossil fuels, better recycling and, last but not least, recarbonisation, i.e. the reabsorption of CO2 by the hardened, finished concrete itself.
MC know-how driving new standards
Research in the field of concrete additives is also now having to be refocused and scaled up. MC is well positioned to act in this respect – as demonstrated by its past research into climate-compatible building materials. The resulting development of a broad range of innovative products, such as cement-free annular gap grouting mortar or cement-free EFC concrete, is clear evidence of its innate capabilities. In addition, MC is currently working in the SABINE research project (more on this in the “Sustainability” section on page 12) with research institutions and other companies on the utilisation of steelworks slags as binding agents for geotechnical construction materials.
Ultimately, the brief for MC’s experts is to compensate as far as possible with newly formulated additives for the properties missing from the new building materials. Because one thing is already certain: The new concretes are bound to require a significantly higher degree of intermediate and curing treatment. With formwork stripping strengths being reached later, curing accelerators such as the products of the MC-FastKick series, and also MC-PowerFlow high-performance superplasticisers based on the latest MC polymer technology, could become ever more essential as enhancing admixtures in the future.
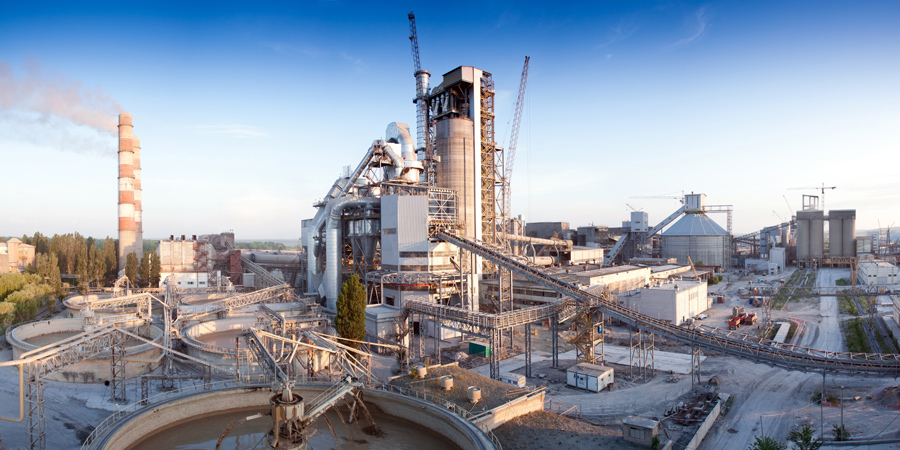
© dmitrykobets - stock.adobe.com
-
Novinky
Kliknite sem a pozrite si aktuálne novinky.
-
Časopis
Kliknite sem a pozrite si aktuálne vydanie nášho firemného časopisu MC aktiv.
-
Downloads
Tu nájdete všetky technické listy k našim produktom, ako aj rôzne prospekty a návody.
-
Referencie
Kliknite sem a pozrite si naše aktuálne referencie.
-
Kariéra
Aktuálne ponuky práce
-
Kontakt
Kliknite sem, aby ste sa dostali ku kontaktom.